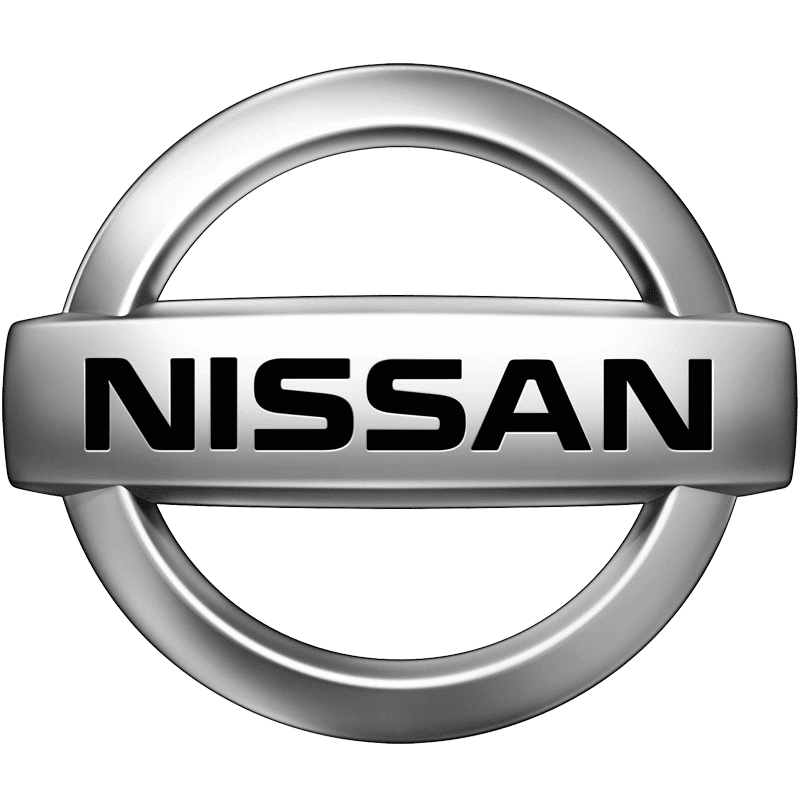
Nissan Cuts Annual Cooling Costs by $490,000 with Xpress®
tekWorx converted the plant’s hydronic configuration to an Integrated Primary-Secondary® (IPS) design and used adaptive control algorithms to provide additional energy savings, save kWh and improve operational efficiencies.
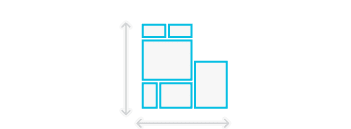
Facility Bio
- Canton, MS
- 4.7 million ft²
- Manufactures Altima, Titan and Murano vehicles
- 10 x 2,500 ton chillers

Situation
- Corporate energy initiatives to reduce energy spending prompted optimization projects
- Plant configured using an inherently inefficient Primary/Secondary hydronic design
- Existing control system was functional, but had no optimization sequence in place
- Plant controls were being operated manually
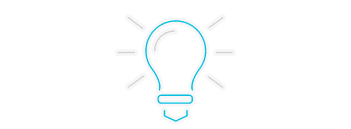
Solution
- Convert plant hydronic configuration to Integrated Primary-Secondary® (IPS)
- Implement Xpress® optimization platform on Nissan standard PLC
- Xpress® adaptive algorithms continuously adjust system operation in real-time, maximizing overall plant efficiency
Results That Exceed Client Expectations
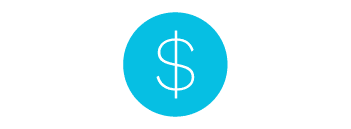
Financial Savings
- $490,000 annual savings
- 1.5-year payback
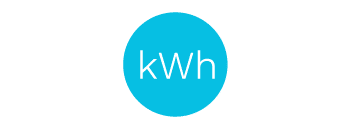
Energy Impact
- 8,500,000 kWh saved annually

Operational Benefits
- Less equipment wear and tear
Operators freed up for other tasks - Automated system controlling all plant equipment
- Chiller health monitoring system provides alerts for preventive maintenance actions
Start saving on cooling costs.Calculate your savings instantly.